This Blog Is Brought to You by Your Ears
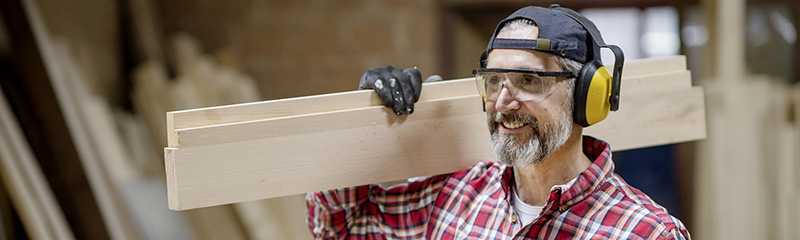
Prevent permanent hearing loss in the workplace with these safety measures.
Can your office phone damage your hearing? What about your building’s smoke detector? Your lawn mower or leaf blower?
Sound level is measured in decibels (dB), ranging from zero to over 140, the threshold of pain. While an average office telephone has a safe sound level of 80, other common sound sources can be more damaging. Prolonged exposure to a smoke detector alarm (85) could cause long-term damage. Meanwhile, even short-time exposure to tools like saws, lawn mowers, and leaf blowers (100–130) can lead to hearing loss.
Exposure to high levels of noise can cause permanent hearing loss in employees. If your business operations involve working in a loud environment, you should implement safeguards to reduce hearing loss.
What Is Hearing Loss?
Under OSHA standards, hearing loss occurs when a person experiences a standard threshold shift (STS) in their hearing ability. The worker takes a baseline audiogram. If the hearing threshold changes in follow-up audiograms, the individual has experienced an STS.
Evaluate Sound Levels at Work
First, conduct a sound level survey to assess the noise level of your operations. NJM’s loss prevention representatives will perform or recommend reliable outside companies to conduct the survey for NJM Business Insurance policyholders.
If the time-weighted average is equal to or greater than 85 decibels (dBA), the company should establish a Hearing Conservation Program.
Control the noise level to stay within the following parameters:
Duration per day, hours | Sound Level dB |
---|---|
8 | 90 |
6 | 92 |
4 | 95 |
3 | 97 |
2 | 100 |
1½ | 102 |
1 | 105 |
½ | 110 |
¼ | 115 |
Implement a Hearing Conservation Program
These basic steps can help you monitor and prevent hearing loss in your employees:
-
Identify employees exposed to noise at or above 85 dB averaged over 8 working hours.
-
Administer baseline and annual audiograms for identified employees, including those hired after the program started.
-
Monitor for changes in production, process, or controls that may increase noise exposure.
-
Train employees in the use of hearing protection, including hearing plugs and muffs, and require their use.
-
Regularly assess the effectiveness of hearing protection and replace faulty instruments.
-
Take steps to reduce sound levels, using tools such as baffles, enclosures, or other engineering controls.
-
Reduce the time of exposure to the sound.
Document all elements of your Hearing Conservation Program, including baseline and annual audiogram levels and training activity. Maintain employee records for the duration of the individual’s employment.
This and other loss prevention topics are included in NJM’s Safety Program Guide, which NJM Business Insurance policyholders can access through their agent or a loss prevention representative. Visit Loss Prevention to read more safety articles, request a safety presentation or materials, or access our selection of streaming safety videos.