Skilled Worker Shortages in Construction
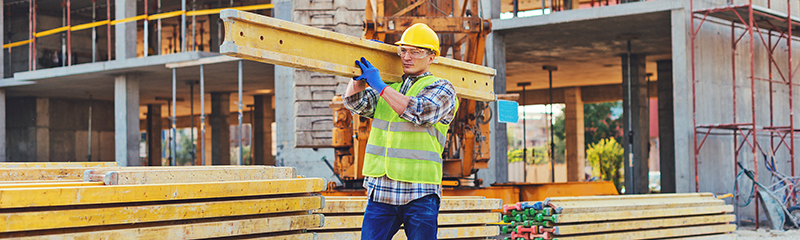
Skilled worker shortages are a concern for many companies in the construction industry. The risks associated with lack of skilled workers are numerous, from worker safety to the quality of the workmanship of the delivered product. However, even a very experienced worker that is perceived to be “skilled” can have a “bad day”. In order to alleviate this issue, a company should take a proactive approach realizing that not every worker is equally skilled.
The COVID–19 crisis has added another dimension to worker safety. As states reinstate construction work for non–essential projects, the risks are even more complicated. To protect workers, employers must now account for COVID–19 in addition to other injuries and potential illnesses. It is essential to integrate all aspects of worker safety into all areas of the job.
Employers should take the following actions:
Train all employees to identify and reduce risks. Ensure that all workers receive training to recognize hazards and become competent in safe work practices. In addition, every employee should have site-specific safety training for every new worksite that they are assigned to. Training should occur upon hiring as well as regularly throughout their employment. More experienced workers should be given a leadership role in mentoring less experienced (or less skilled) workers.
Create ways to get all employees enthusiastic about their work. When employees are passionate about the work they are doing, they’re more likely to be careful on job sites. Increasing employee morale and making safety part of the company culture will help to reduce risk–taking behavior. Additionally, invest in employees’ training and exploration of the industry. This gives employees insight into how their work contributes to projects and broader initiatives.
Eliminate any question marks. Encourage new workers to ask questions about tasks or procedures that are unclear or not understood. Consider implementing a mentoring system for new employees, where an experienced worker is available to answer questions, help them learn the ropes, and support their professional growth. Provide a line of communication between field workers and members of management in which a field employee could have a comfort level confiding in people other than their immediate colleagues.
Machine and equipment operations. Ensure that all workers are properly qualified to operate the respective machinery or equipment that they are being tasked to use. Proper qualifications can come in the form of writing, licensing, or a company decision based on the experience of the worker. A designated person within the company can decide that a worker may operate machinery or equipment by virtue of their experience.
Outline next steps should an injury or “near miss” occur. Make sure all workers know how to appropriately report incidents if they are hurt on the job. “Near misses” should be reported as well. This will help you to identify and investigate any underlying hazards that may need to be addressed.
This document is designed to provide for suggestions and guidance. Regardless of individual situations, it is always imperative that you do not skip steps or abbreviate trainings. It is essential to adequately prepare the incoming workforce for the risks of the job.