4 Keys to Safety in Manufacturing
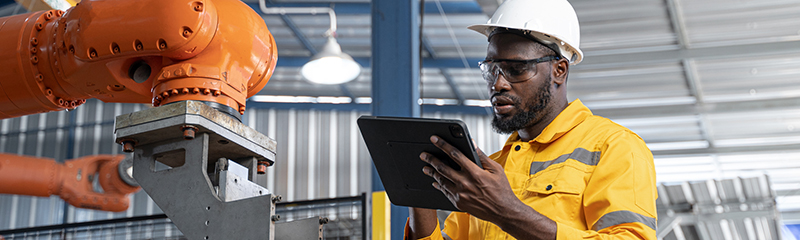
Manufacturing employees work with hazardous materials, heavy machinery, and dangerous substances that can lead to injuries and illness. Establishing a culture of safety in your workplace can help protect employees, avoid potential repair costs to facilities and machinery, and control the cost of insurance.
Here are four key steps to implement your safety efforts in the workplace.
1. Employee Training
Train new employees before they assume their daily responsibilities. Identify all potential hazards and emphasize the importance of safety equipment. Employers should also encourage employees to report any dangers they observe on the job.
Make sure safety in the workplace remains top of mind for all manufacturing employees through use of signage and recurrent workshops, online training, and site assessments.
2. Machine and Equipment Care
Regular cleaning and maintenance of machinery can help protect employees from injuries caused by machine malfunction or failure. Assign daily inspection of all machinery and safety equipment to an employee or team of employees.
Stay attentive to proper use of machinery and implement regular training. Misuse of equipment is a leading cause of workplace injury for manufacturing companies.
3. Emergency Preparedness
Incidents can occur unexpectedly, so it is essential to develop your plan for workplace emergencies. Identify the most probable emergency situations by taking into account hazardous materials, machinery, and the worksite layout of your manufacturing company. Educate your employees on how to respond to different types of emergencies and assign individuals to recovery tasks.
Each emergency plan should include:
-
Designated safe spaces
-
Evacuation procedures
-
Strategy for loss of power
-
Awareness of fire extinguisher and first aid kit use and locations
-
A comprehensive communication plan
4. Personal Protective Equipment (PPE)
PPE is critical in the manufacturing industry. Its benefits include protecting your employees from injury and illness, productivity, OSHA compliance, and strengthening the culture of workplace safety.
Provide the appropriate PPE for all employees specific to their job responsibilities and enforce rules that require the proper use of PPE on the job. Common protective equipment includes gloves, hard hats, safety glasses, and ear plugs.
NJM was established more than 100 years ago and has remained committed to providing reliable, cost-effective, and safety-focused insurance. All NJM business policyholders receive access to loss prevention resources to help reduce injuries and illnesses in the workplace. Connect with an agent today to get a quote for NJM Business Insurance.
References:
9 Safety Training Ideas for Manufacturing Employees. EduMe. edume.com
Emergency Preparedness and Response: Getting Started. U.S. Department of Labor. osha.gov
The information contained in this article should not be construed as professional advice, and is not intended to replace official sources. Other resources linked from these pages are maintained by independent providers; therefore, NJM cannot guarantee their accuracy.